
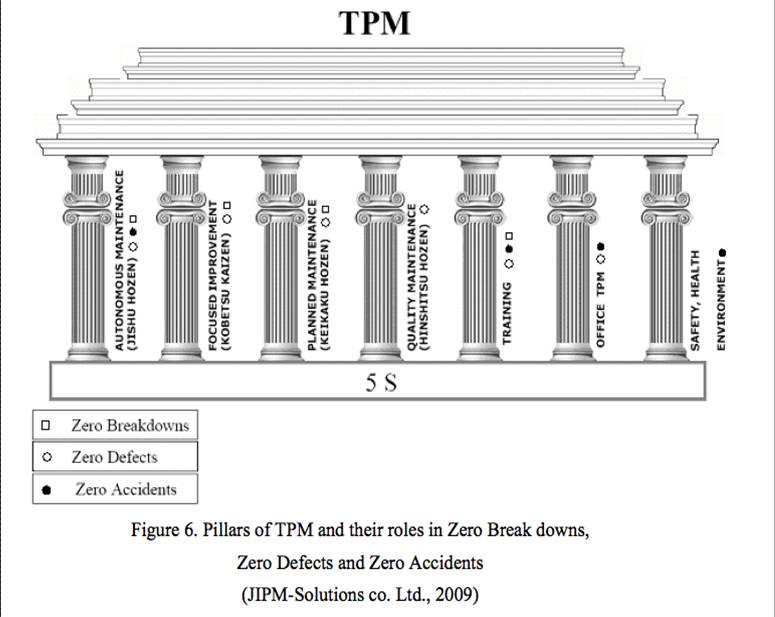

However, they can still benefit from the core idea of TPM – involving operators in equipment maintenance. Many organizations aren’t ready for such a commitment. Reaching that level can take years of continuous improvement. The ultimate goal of implementing TPM is to get an organization as close as possible to perfect production: zero defects, zero breakdowns, zero accidents, and zero waste. Having trouble? Contact customer support at (855) 226-0213 or at OK Stopping at autonomous maintenance It looks like you are using a personal email address. Our resource library is available for free to professionlas and students. This leads to the creation of company-wide proactive maintenance culture and the development of efficient preventive maintenance procedures. Each pillar focuses on optimizing a specific part of maintenance operations or quality management. When that is in place, the organization can start implementing the pillars. The 5S system outlines best practices employees should follow to eliminate wasteful actions, standardize common procedures, and ensure that the working environment is always clean and organized. It lays out a robust framework that is represented by the 5S foundation and eight pillars you can see in the image below.Īny implementation of total productive maintenance is doomed to fail if it isn’t built upon a strong foundation, which is achieved by employing the 5S methodology. TPM was developed by Seiichi Nakajima in the late 1950s. Total preventive maintenance is used as a synonym for total productive maintenance. The idea is that people who operate the equipment can be upskilled to perform routine maintenance tasks on “their” machines.
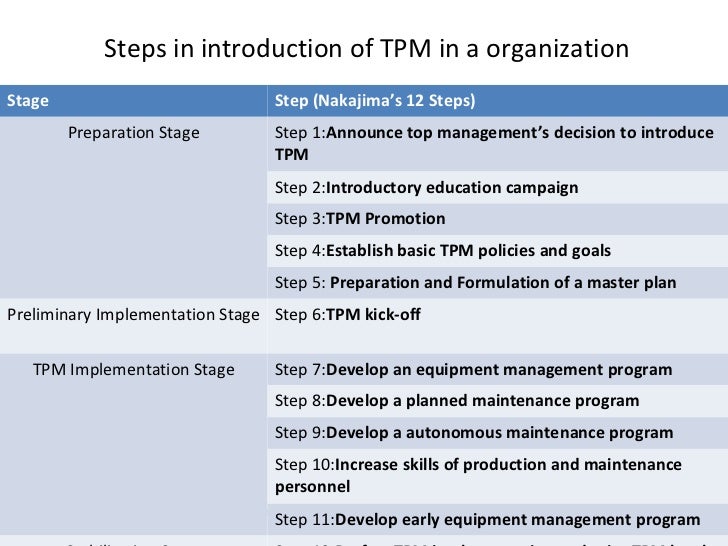
What is unique to TPM is that it empowers machine operators to take on basic maintenance responsibilities. Total preventive maintenance represents an organized, standardized, and structured approach to preventive maintenance. The essence of total preventive maintenance (TPM) Total preventive maintenance recognizes that and offers a framework to expand the maintenance responsibilities across the production floor.Īn increasing number of manufacturers are trying to implement TPM in an effort to lower operating costs, reduce downtime, and improve OEE. In a truly efficient organization, asset care cannot be the sole responsibility of the maintenance team. AugThe What and Why of Total Preventive Maintenance (TPM)
